ScanTech Offshore (James Fisher and Sons)
ST3100 – Safer, Stronger, Smaller
A world-class innovation from ScanTech Offshore is helping to double capacity while more than halving the footprint on a vessel as the company launches its ST3100 air compressor which delivers Class Zero, oil free air for big bubble curtain applications around offshore wind farm developments. VP of North America, Barry Craig tells Energy Focus about expansion in the growing US market.
The potential of offshore wind as a green energy source is unmatched. The IEA suggests that worldwide, offshore wind could provide around 36,000 TWh of electricity each year – close to the total projected global demand for electricity in 2040. The industry is expected to become a US$1 trillion (£800 million) sector in the coming decades, and world-leading economies including the US are set to realise the booming potential of the wind energy market. In 2018, US electricity demand was 4,011 TWh but the potential of offshore wind was calculated at 8,086 TWh. Turbine technology is getting bigger and cheaper, and regulation is paving the way for sustainable rollout.
In the US, where 30GW is targeted by 2030, less than 0.5GW is currently installed, but that is changing. Project developers are continuing to search for exciting opportunities and a robust supply chain is being developed.
From north to south, all the way down the US East Coast, offshore wind farms are proposed or already planned. To ensure the public benefit from not only the green energy that will come, the Jones Act enforces the deployment of local vessels and workforce (where possible) to carry out construction activities.
Barry Craig, VP North America
James Fisher and Sons, headquartered in the UK, and its subsidiary ScanTech Offshore, has an existing operation in Houston, Texas, and recently expanded to Providence, Rhode Island to further support the nascent US offshore wind industry. It is also expected in 2024 that further expansion of supporting facilities will be opened across the North-East Coast of the US. These operational bases will provide in-country support of ScanTech Offshore’s world-class bubble curtain air delivery packages.
In 2018, ScanTech Offshore – a company with a strong history in well-test and support for the oil and gas industry – diversified and entered the renewables market, exploring opportunities for the deployment of its specialist air compressor units. Through bespoke technology which was carefully engineered to be powerful but stackable on a vessel, ScanTech Offshore air compressors quickly became recognisable across the energy sector as a reliable, premium product.
Engineers at ScanTech Offshore sites in Aberdeen and Great Yarmouth quickly saw the potential of air compressors in wind energy, supporting the idea of the bubble curtain – a barrier that surrounds the piling of wind turbine foundations with bubbles to attenuate noise and protect marine wildlife. Air is sent down a hose to a flexible hose system, which is pre-laid on the seabed with special nozzle openings that release bubbles in strategic column formations.
A high flow of compressed air is required to create a well-formed and effective bubble curtain. Not as simple as pumping gas down a tube, the air that goes into the water must be Class Zero ‘clean air’ and must be moved in huge volumes at pressure. To create the force, ScanTech Offshore stacks up multiple compressor units alongside its SeaSentry system, which ensures air is contaminant-free and leaves no negative environmental impact in the water.
Prior to ScanTech Offshore, bubble curtains delivered the volume of compressed air by installing many industrial-style air compressors that required a large footprint on a vessel (up to 30 air compressors on a single vessel). This resulted in the need for the deployment of larger vessels (typically PSVs) in order to install the required compressed air volume needed to support an effective bubble curtain.
The typical compressor types being deployed were either not stackable due to the inability to stack or issues resulting in overheating due to the types of vessels often available in the market to locate the equipment.
ScanTech Offshore successfully entered the market in 2018 by providing the market-leading bubble curtain specialist – HydroTechnik Lubeck – a ‘stacked solution’ that effectively reduced the footprint allowing for a larger portion of available vessels to be considered to support certain offshore campaigns. This was achieved by deploying ScanTech Offshore’s containerised ST1600 (1600cfm / 45m3/min) model air compressor that had been proven to be a durable and reliable compressor from supporting high-value well test support contracts in the oil and gas sector for over 25 years.
ScanTech Offshore has supported numerous Big Bubble Curtain (BBC) projects spanning from the UK, and Europe to Asia deploying the ST1600 compressors with great success. However, during this time, it was clear to ScanTech Offshore that the market needed a truly purpose-built solution that would eliminate the most common challenges experienced when installing a large spread of diesel-driven air compressors on a vessel with confined space constraints.
Previously, compressors would give off undesirable levels of heat whilst working on ships with high sides, as the heat from machinery would struggle to escape. Temperatures became uncomfortable for personnel and led to increased maintenance for machinery. It became clear that future projects may even require larger volumes of compressed air to support an effective bubble curtain, due to challenging environmental conditions (such as strong sea currents) and the increasing size of the foundations (requiring more noise attenuation).
HydroTechnik approached ScanTech Offshore for a solution that would provide further deck space savings allowing for even higher volumes of compressed air to be installed on a single vessel but also “fit for purpose” whilst working on vessels with high sides. Finally, the new system needed to be capable of supporting projects in deeper water – capable of producing a higher working pressure was of critical importance.
ST3100 CREATION
After refinement and much testing, ScanTech Offshore developed the ST3100, a 20ft CSC / DNV2.7-1 containerised air compressor with a Caterpillar engine and original radiator technology that can deliver 3100cfm and capable of working pressures of up to 200 PSI, providing the air required to a create a bubble curtain that reduces noise by up to 90%. Importantly, the ST3100 delivers more than double the power compared to previous air compressors, whilst taking up half the footprint, even when equipment is not stacked. When stacked (as per the design) the footprint savings are much greater providing up to 3-4 times more compressed air on the same footprint as some of the alternative solutions available in the market.
Testing and learning in 2018 through to 2022, several major projects were undertaken as ScanTech Offshore eyed eventual rollout in the US. “Even during the initial learning in Europe and Asia, we instantly saw that the market needed a purpose-built solution and not just a compressor. It had to be reliable, and it had to be designed first and foremost with the safety of personnel in mind,” says Barry Craig, VP of North America at ScanTech Offshore.
He says that on an oil rig, compressors are stacked in a uniformed position and the heat generated can escape. But on the back of a vessel, the heat has nowhere to go, and the result was increased maintenance in addition to the need to take additional measures including sea water cooling for the units when working in higher ambient countries such as Asia.
“We spent 18 months on the design work, and we looked at many different options to maximise every aspect, from power to emissions.”
Caterpillar engines were chosen because they were familiar and proven in the harshest environments that ScanTech Offshore support, this paired with ScanTech Offshore’s vast experience with the engines made them the ideal choice. The engines also offer Stage V / EPA Tier Four Final emission standards – required for compliance in both the European and US markets. There is also no need for additives, meaning no storage of diesel exhaust fluid (DEF) on a vessel. Pairing with compressor technology from Sullair, the offering was almost complete, but ScanTech Offshore still had to develop the solution to deal with the high temperatures.
“We came up with a unique heat rejection system that has been incorporated into the compressor unit that allows it to be stackable, reducing footprint drastically, and ensuring that the ambient conditions around the machinery and on the vessel are maintained well within safe working limits for personnel. Furthermore, the solution providing additional value through automated refuelling and reduced need for personnel amongst other things.”
With extensive and successful trials conducted on the ST3100 solution, the team took the units to the US market and successfully supported the first commercial scale offshore wind farm on the East Coast of the US. The ST3100 solution ensured our client could deploy their own specialist vessel for the project, negating the need to deploy a much larger vessel to the project at a greater cost.
Alongside the cost-effectiveness proven in the US, the ST3100 did the job underwater, reducing decibels from construction activity significantly, protecting whales, dolphins, porpoises, and other sea life. On the deck, the heat from the units was completely mitigated thanks to the clever system designed by ScanTech Offshore.
SAFER, MORE EFFICIENT
The process of evolution from compressor for oil and gas, to all-new specialist designed product for renewables was a journey for ScanTech Offshore. “We had to go into it almost with our eyes closed to learn – what do we actually need on these vessels to make it safer, more efficient, and maximise performance? At the end of the day, this is all about uptime,” says Craig, adding that downtime can cost millions of dollars per day. “The value of us providing what we do is critical. Everything stops if we’re not providing compressed air to the bubble curtain effectively.”
The offshore project in the US provided engineers and offshore teams with a significant amount of data to display to the market. The on-deck and beneath the surface excellence displayed on this key project in the US was the perfect case study to demonstrate the full value that the ST3100 solution offers.
Craig moved to Rhode Island in 2022, with plans to deploy the ST3100 technology along the East Coast of the US, supporting their key clients and partners in each state. Following the successful deployment on the recent US project, it has set the business up as a well-established player for the future projects expected in region.
Now a proven part of the growing supply chain, ScanTech Offshore hopes to ramp up US involvement substantially. “We want to be the number one supplier for sure. We have taken the design which we built in the UK, and we’ve taken it across the pond with a leading EPCI to do the work on the US East Coast, and it’s been very successful,” says Craig.
Already secured on two large projects for the next two years, local manufacturing will begin imminently with the US renewable pipeline now beyond 51GW – enough to power 20 million homes.
“We focused on the US because it is an emerging market and it’s good to be in emerging markets at the start,” says Craig, adding that the importance of local procurement is vital. “We already had our facility in Houston with a team which has successfully supported operations in the US for over a decade. The same team even supported operations on the first US offshore wind turbines off Block Island, RI. Today, with the expanding offshore wind ambition demonstrated by the US, we also have plans to replicate and expand our offering up and down the East Coast to support the upcoming projects.
“We will work collaboratively with key partners in region to ensure our air delivery packages can support the projects and bring a huge amount of added value through our innovative technology. We are working with our partners on methods to improve efficiency and reduce cost in an effort to further boost the sustainability of the offshore wind industry.”
Craig, pays tribute to the James Fisher and Sons plc board who backed the move during an unpredictable time, following the pandemic and global supply chain challenges, providing investment and continuing to support the team at ScanTech Offshore.
“We are now set to enter phase 3 of our build programme where equipment will be assembled out of our Houston facility. The units being built will probably be working on renewable based projects for the next decade at least. We will build the compressors in America, with 100% US content.”
BIGGEST IMPACT
The US market is different to the European sector and one of the challenges is vessel size and availability. The Jones Act means that locally flagged vessels, manned by local people, must be used in offshore construction, and this can mean big changes in cost as projects look to move up in size. To help here, ScanTech Offshore always had the footprint of the compressor in mind and Craig says that making it as small as possible without compromising on power was the goal.
“We want to give a solution that widens the selection process for a vessel that can be used and allow vessels to potentially complete other tasks as there would be spare deck space,” he hopes.
“When we look at the vessels available here, there’s not a huge number of large vessels and the availability of vessels is not great because the oil and gas market is up. The day rate jumps from vessel to vessel and can easily be $10,000 – $15,000 a day if you need to jump up to the next class.”
“In some circumstances, ScanTech Offshore technology has the potential to even to reduce the need for two vessels,” reiterates Craig.
The US offshore wind developers have been strict in saying you must comply with the highest level of tier emissions, and you must use US-flagged vessels. We looked at the market and how it might work, and we believed that the ST3100 could make an impact there more than anywhere else in the world by reducing the footprint and allowing for a wider variety of Jones Act vessels to be deployed. If a competitor tried to stack the equipment, then you’d get the same issue of heat not escaping and ambient temperatures rising beyond what you would want for people or machinery. The ST3100 not only stacks but conforms to the slim profile that US vessels typically have ensuring there is no dead space when installing equipment.
The added bonus for ScanTech Offshore equipment is the certification that boosts confidence. Everything is rated for offshore work – DNV 2.7-1 certified and CSC approved, using the correct grade of steel, easy to transport and crane like any other container. “We give validation that everything is fit for purpose and designed to be on a vessel and designed to be at sea,” says Craig.
“Previously, industrial compressors had been chained to the back deck of a vessel, and no formal certification such as CSC were being met. With the ST3100, walkways are clear, and units can be craned from vessel to vessel if required,” he adds.
On-ship, with temperature levels low, and you are automatically informed if maintenance issues could arise via remote telemetry installed on all units (creating reports for the client at the same time). ScanTech Offshore engineers are thrilled with the performance of the ST3100 units to date. Craig reports that, ultimately, they continue to do the job.
“I speak with our team on the project, and they say they have never seen so many whales, ever. The number of whales off the East Coast of the US is phenomenal. The project we recently supported was stopped several times in the name of animal welfare. We hear of in excess of 100 whales at a time in a single area and that is not something our team sees often. So, I think you can see why they’ve adopted the highest levels of mitigation possible.”
BUOYANT INDUSTRY
The wind energy market will grow exponentially in the coming decades and Craig is excited to be part of a solution for the future. In the US, new vessels are on order or under construction, new facilities are being erected, domestic skills development programmes are being rolled out, and the American Clean Power Association (ACP) expects 83,000 jobs to be created in offshore wind by 2030.
“With the rapid expansion of offshore wind globally across multiple geographies, it highlights the necessity to build and support locally in order to be successful,” says Craig.
Typically, sound detection buoys are placed at 750m distances from a construction site and operations must not exceed the agreed threshold in the environmental permit which is critical to comply with at all times. The bubble curtain helps to achieve this by altering the characteristics of the sound waves as they pass through the bubbles.
“There’s nothing that gets close to it in terms of noise reduction,” confirms Craig. “A 15-18-decibel reduction is enough to make a real impact as sound behaves differently in water. This can equate to a 90-95% noise reduction which provides a clear benefit for marine life.”
Other noise abatement technologies can be used alongside the bubble curtain to protect marine life and, as long as conditions are suitable, the local underwater populations will remain well protected as activity ramps up. However, time after time it has been shown that bubble curtains are the most effective technology to attenuate noise during pile driving activities.
“It’s phenomenal, it has been a massive team effort from the offshore teams feeding in the information to our engineering team doing a lot of testing. We’ve just finished a big job, one of the first in the US and it has been a great success. You can do all the simulations, but until you prove it in the field, it’s only as good as your theory.”
Going forward, ScanTech Offshore is well-placed for expansion in the US and harnessing potential in the Blue economy, and Craig hopes that the wider James Fisher and Sons team, which has already supported over 17GW of renewable construction and development around the world, can assist as the nation ramps up effort to green its generating capacity.
“We’ve already secured a further two major projects on the East Coast of the US for major international wind energy businesses. Our pipeline here is extremely exciting for at least the next three years, complementing our already prominent Europe and Asia business lines.
He adds further assurance that if you engage with ScanTech Offshore, or the wider James Fisher Group, you will get a partnership that achieves results.
“We’ve all been offshore, and we’ve seen the failings of our customers, competitors or even our own. That’s what differentiates us, and that is why we are successful.
“Our units are brand new; they’re not going to have been in anybody else’s hands, and they’re not going to be rented out without our people.”
Truly a leading product for a burgeoning market, ScanTech Offshore’s ST3100 is an enabler of the green energy transition in the US. All EPCI companies and fleet owners should be considering the significant efficiencies that the system offers. Asked if he is expecting competitors to flood the market with similar products anytime soon, Craig remains confident.
“By the time they do, we will likely be on to the next innovation by working closely with our partners and clients as we all strive to further improve efficiency.”
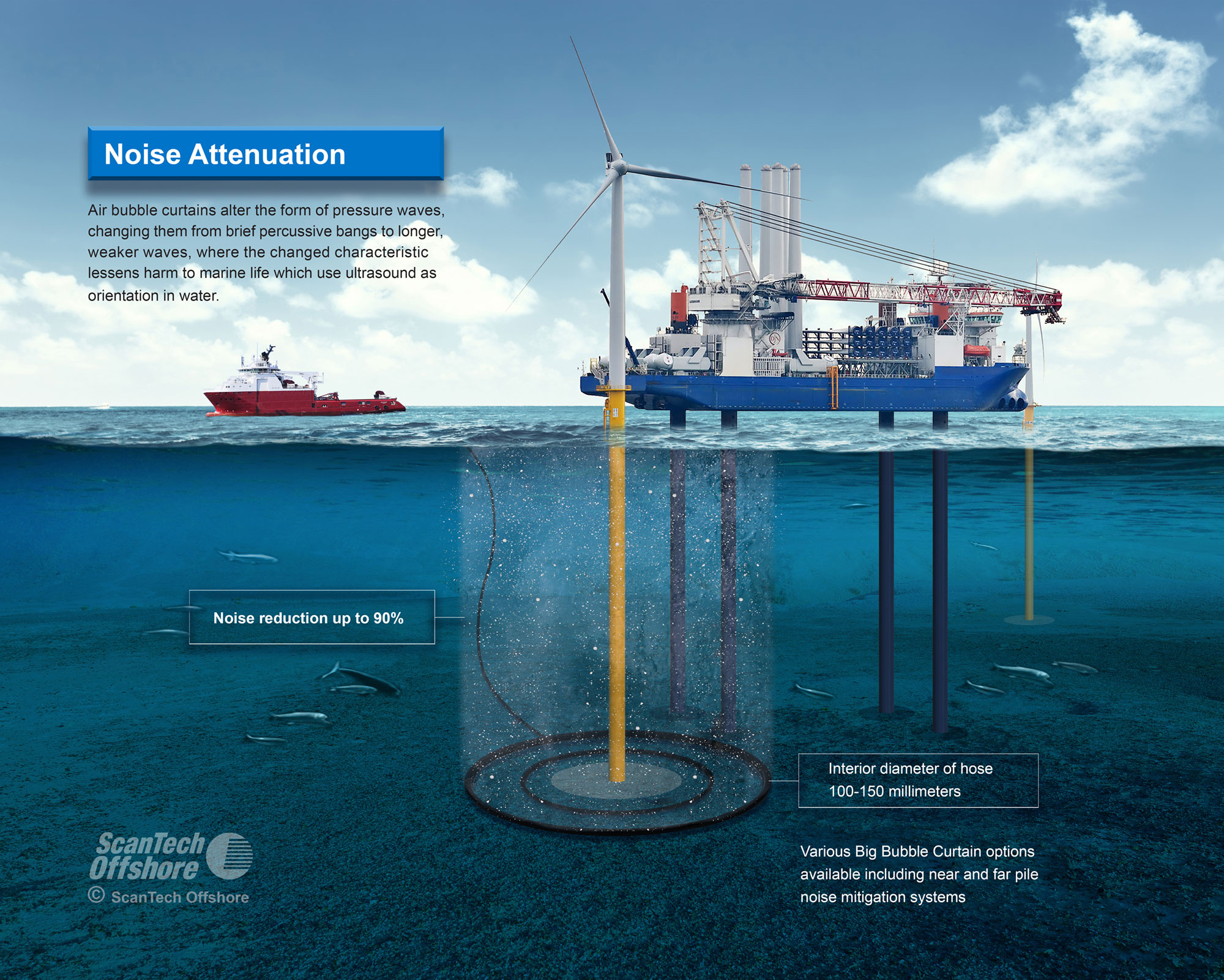